COVID-19: Trickle Down Effects of Coronavirus on the Construction Industry
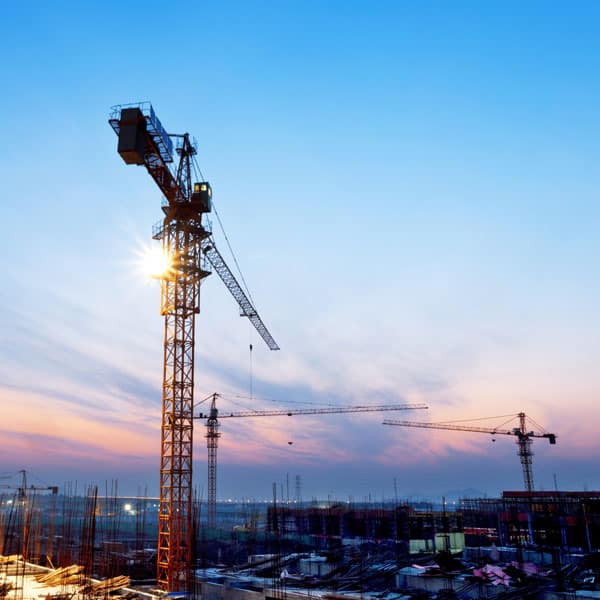
GlassRatner recently published COVID-19: Managing Construction Delays Amid the Coronavirus Pandemic, which was the first in a series of articles related to the coronavirus pandemic. The article discussed issues facing project stakeholders in managing capital projects through the current health crisis. This article, the second in the series, will discuss the differences between the coronavirus pandemic and other events that have traditionally triggered force majeure claims. It will discuss why the current situation could create the potential for more drastic material and labor shortages and price increases, which might force projects to treat all procured items as long-lead items.
Force majeure events, such as unusually severe weather or labor strikes, typically have clearly identifiable start and end dates, as well as relatively easily definable damages. While pandemic-related government restrictions, such as stop-work orders, may also have clear start and end dates, the overall effects are much more widespread. The days preceding and following the force majeure events are quite different in each scenario:
- Labor strikes have little to no damages leading up to the strike – work progresses as normal up until a sudden stop. Damages are typically limited to the lost days during the strike and the associated costs of expediting work to regain lost time. Once the strike is resolved, work continues in full production.
- Severe weather, such as hurricanes, is typically forecasted days in advance. While project teams may decide not to start certain activities, such as an excavation, in the days leading up to a storm, work continues with few impacts until a day or two prior to the forecasted event. At this point, the teams work to clean the jobsite, secure materials, protect equipment, and ensure team members can get home safely prior to the storm. Once the storm has passed and it is safe to return to work, the physical damage is assessed. The costs of such an event are limited to the efforts prior to the storm, the damage incurred during the storm, and the re-work or cleanup required after the storm. Following a typical storm, the disruption to the supply chain for materials and equipment is often limited and short-lived. An exception is in the case of an extremely severe storm, such as Hurricane Katrina, where devastation to infrastructure may impact labor and material availability along the path of the hurricane long after the storm clears.
- The current pandemic is proving to include the broadest impacts. While a project may have an easily quantifiable period of zero production due to a government stop work order, some construction projects are considered “essential” and will not be included in such a restriction. Regardless, all projects may be affected by the gradual reduction in workforce as the pandemic worsens. Many key team members may, if they have not already, be unable to travel to the site due to government restrictions, personal risk tolerance, or their individual health concerns. Assuming projects are not shut down, project teams will need to focus on critical path activities during the time of decreased labor, using less-efficient hybrid crews comprised of the craft labor who are able to work. Delays to many non-critical path activities will likely be inevitable. Unlike labor strikes and severe weather events, there may not be one day where the entire team returns to work and normal activity resumes; rather, it will most likely be a gradual return to normalcy. Additionally, there will likely be shortages of tools, equipment, and materials that could last for months after businesses return to work.
Severe weather events can devastate relatively large areas, and lead to massive evacuations and physical damages. While not diminishing the breadth of any severe weather event, the effects of a hurricane, flood, earthquake, or wildfire are typically regional. So too are their effects, such as reduced labor availability, lack of housing for laborers, limited utilities, higher paying jobs for cleanup/repair, and transportation and communication issues.
The important difference with the current pandemic is that it is a global event; every project and every economy worldwide is being affected. The fact that a pandemic does not leave a path of physical destruction only makes it harder to quantify the damages. Buildings and manufacturing facilities are being repurposed, or closed, to aid in the fight. While the infrastructure is not destroyed, it is not producing the same products or quantities on which construction schedules rely. The impacts will likely continue delaying and disrupting the projects for a much longer period, long past the “end” of the pandemic.
Shortages will affect even “essential” construction projects. There is clearly a shortage of personal protective equipment (PPE) for medical workers, and contractors have already heeded the call, donating their supplies of face masks, gloves, etc. (thank you to all who were able to donate!). While the manufacturing of these supplies has since ramped up, it is unknown when construction teams will once again be able to refill their stockpiles.
Even if a construction project can continue work with limited supplies, these projects are facing new challenges and additional costs. Many drastic measures are currently being implemented to keep projects operational and employees safe. These include resequencing work to spread out the employees’ tasks, hiring cleaning crews to disinfect and sanitize all surfaces daily, and implementing alternative processes to manage the shortage of PPE. Even if a project itself is “essential,” its fabricators and suppliers may have been forced to shut down operations, which may lead to the subsequent delay of critical activities on site. There may be alternate distributors or alternate products which are available for “off the shelf” items, but both may result in a higher cost to the project.
Construction projects, especially the large EPC contracts, rely on worldwide resources, including engineering, fabrication, and materials. Due to the global scale of the pandemic, distribution has been affected by the coronavirus. Shipping has been delayed, especially from China, as ports implement measures to slow the spread of the virus.
As these worldwide economic effects are being felt, construction is slowing or halting, and some contract start dates are being pushed, which may lead to bankruptcies. Governments are approving relief bills as employees across all business sectors are being furloughed or laid off. Such broad effects are not the typical results of force majeure events such as labor strikes or unusually severe weather.
As a result, many companies, including GlassRatner’s clients, are looking to their contract’s force majeure clause as a source of contractual relief. It is important to remember that typically the premise of force majeure is that none of the parties in the contract should be liable for delays associated with an event that is outside of its control. In addition, whether force majeure is a compensable event is typically defined in the contract. However, while no party may be liable, the associated costs will likely be incurred by all parties. GlassRatner has expertise in force majeure claims on projects around the world and can help companies evaluate their claims position and protect against additional exposure.
There will certainly be many “lessons learned” from this pandemic, as the current situation is unprecedented. Please check back soon for the next article in this series on the coronavirus’s effects on construction for more on how project stakeholders may want to rethink force majeure clauses in future contracts as a result of this pandemic.
Author: Matthew Scheps